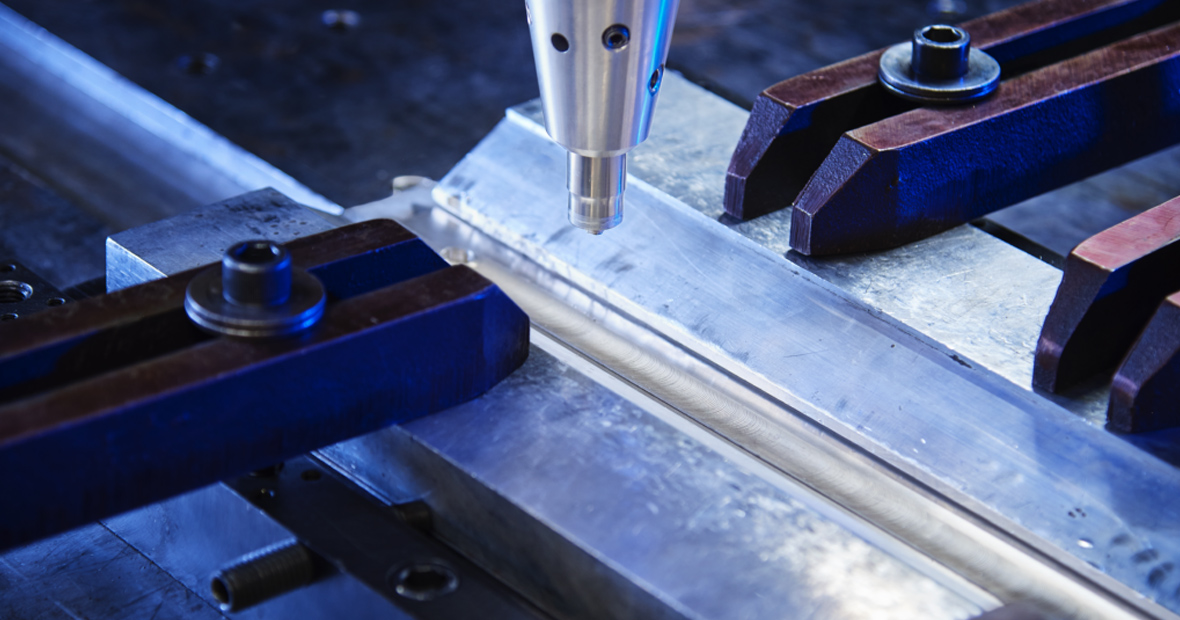
Within the realms of modern manufacturing, a process known as friction stir welding has been steadily gaining recognition for its myriad of advantages. This innovative process boasts enhanced mechanical properties, environmental benefits, energy efficiency, and broad applications from aerospace to automotive industries. On the flip side, understanding the inherent limitations and challenges associated with friction stir welding holds equal significance. Issues of material suitability, technical difficulties in tool design, machine capabilities, cost implications, and technology accessibility all play a role. This article delves into these aspects while providing a comparative analysis against traditional welding methods and discussing recent innovations in tool design and material compatibility within the Friction stir welding process.
Exploring the advantages of friction stir welding in modern manufacturing
Friction stir welding (FSW), an innovative technology applied in modern manufacturing, boasts numerous advantages, enhancing the industry's capabilities. FSW technology, an effective joining method, particularly for aluminium alloys, has revolutionized the aerospace and automotive industries by presenting them with new possibilities. The strength of the joints is significantly increased using this technology, thereby optimizing the durability of metal structures and increasing their lifespan.
Enhanced mechanical properties through friction stir welding
With FSW, the quality of welded joints sees dramatic improvement, reducing the requirement for rework and subsequently boosting production efficiency. The welding process operates at lower temperatures compared to traditional methods, thereby minimizing material deformation. This technology further demonstrates its superiority through its capability of joining different aluminium alloys, providing high quality and strength.
Environmental benefits and energy efficiency of friction stir welding
An added advantage of FSW is its eco-friendly approach. It does not require flux or shielding gas, thus promoting greener manufacturing practices. This process's energy efficiency, coupled with its potential for automation, allows for seamless integration into modern production lines, driving increased efficiency. The use of FSW technology undoubtedly champions a sustainable manufacturing future.
Expanding applications : from aerospace to automotive industries
With its impressive capability, FSW technology's applications are not restricted to specific industries. Its versatility and high-quality outcomes have made it desirable in various sectors, including aerospace and automotive. Whether it's the joining of aluminium alloys or ensuring the strength of metal structures, FSW is a key player in modern manufacturing.
Understanding the limitations and challenges of friction stir welding
Friction Stir Welding (FSW) has made a significant impact in the industrial sector. Despite its advantages, certain limitations and challenges are noteworthy.
Material Limitations and Suitability for Friction Stir Welding
One critical challenge involves selecting and maintaining the durability of FSW welding tools, particularly when dealing with high-strength materials. The FSW process faces limitations when used with certain materials exhibiting low ductility or a high melting temperature. Achieving high-quality FSW welds with such materials proves to be quite difficult.
Technical Challenges in Tool Design and Machine Capability
Another challenge lies in managing the temperature and heat control in the welding zone to prevent material degradation. The FSW process also faces speed limitations, affecting efficiency and productivity in industrial applications. Additionally, specific issues arise when welding dissimilar materials, posing challenges in terms of compatibility and welded joint performance.
Cost Implications and Accessibility of Friction Stir Welding Technology
FSW is a complex process that generates residual stress and tension, which may compromise the structural integrity of welded parts. These limitations, combined with the high cost of FSW technology, can hinder its widespread adoption in the industry.
Comparative analysis: friction stir welding vs. traditional welding methods
In the realm of material joining, friction stir welding (FSW) emerges as a revolutionary technology, contrasting with traditional welding methods like laser or arc welding. This comparative analysis delves into various aspects of FSW and traditional welding, ranging from weld quality, environmental impact, cost-efficiency, material adaptability, thermal stress, to application versatility.Looking at the quality of welds, a discernible difference surfaces between the consistency and strength of joints welded by FSW and those executed using traditional methods. FSW yields high-quality welds, outperforming conventional techniques in terms of weld strength and consistency.Environmentally, FSW proves to be a greener option. The technique exhibits lower emissions, energy consumption, and waste compared to conventional welding methods. Financially, initial installation costs of FSW may be steep, yet the swiftness of the welding process offsets this disadvantage over time.In terms of material adaptability, FSW exhibits proficiency in joining a variety of alloys including aluminium, titanium, and steel, highlighting the limitations of traditional methods with certain materials. The thermal stress imposed by FSW is notably lower, reducing deformations in the welded parts, compared to the significant heat generation of traditional methods.Lastly, FSW finds exclusive applications in fields like aerospace and automotive industries, while traditional welding methods display versatility across various applications. In the end, both FSW and traditional methods contribute significantly to the state of the welding industry, each with its unique strengths and weaknesses.
Innovations in friction stir welding tool design and material compatibility
With the advancements in technology, a significant evolution has been observed in the design of friction stir welding (FSW) tools. The primary objective of these innovations is to enhance compatibility with a diverse range of aluminum alloys. The development of innovative materials for FSW tools is another frontier that aims at boosting durability and wear resistance. The new tool design innovations in FSW are contributing to optimizing thermal and mechanical distribution during the welding of metal panels.
Advanced techniques for optimizing the shape of welding tools are being employed to reinforce the mechanical properties of welded joints. These have brought about a revolution in the welding industry by overcoming the material compatibility challenges in FSW of light alloys and metal composites. The use of computer-assisted technologies for the custom design of FSW tools is gaining popularity. The main aim is to achieve better adaptability to specific materials. In the welding realm, it is a priority to enhance the compatibility of FSW tools with different aluminum alloys. This not only improves the quality of the work but also increases the life span of the tools. The constant evolution of the design of FSW tools and the development of innovative materials for these tools have significantly increased their durability and resistance to wear.